Kumovis wants to facilitate a new generation of medical products to give health care the opportunity to create innovative medical technology. To do this, the company uses additive manufacturing, better known as 3D printing – a technology that has been researched in the space sector for decades. An interview with Dr Ing. Miriam Haerst, co-director and co-founder.
Who are you and how did you come up with the idea of Kumovis?
We at Kumovis have set ourselves the goal of facilitating a new generation of medical products with additive manufacturing. Since the company was founded in 2017, our startup has been working on industry-specific solutions based on our 3D printing system, the Kumovis R1. We have developed this specifically to manufacture medical products from high-performance plastics.
The idea for this came to us – i.e. the subsequent founding team consisting of me, Stefan Leonhardt, Sebastian Pammer, Stefan Fischer and Alexander Henhammer – during our studies and research activities at the Technical University of Munich. We were looking for a way to process high-performance plastics, which are already established in medical technology, using additive manufacturing. As there were no satisfactory solutions on the market at the time, we decided to develop one ourselves.
What influence did space technology have on the development of your concept?
The space industry and medical technology place a similar amount of value on the resilience and longevity of additively manufactured products. Quality is a crucial factor that comes into effect when established high-performance plastics are processed in both industries. It is all the more important for Kumovis to make a system available that does justice to these factors and materials.
With a view to the mechanics, we are among the first, for instance, to have succeeded in additively manufacturing products from the high-performance plastic PEEK so that they can be implanted. Knowledge from research in space and medicine has paved the way for us here, as the use of high-performance plastics has been the subject of research in both sectors for decades.
Your 3D printers are now also found in hospitals. How do you assist the hospital staff when using the printer or can they use it independently?
Our service comprises an end-to-end workflow, which extends from DICOM processing (Digital Imaging and Communications in Medicine) to the finished medical product. For clinical applications, Kumovis provides the 3D printer as well as assistance in introducing the entire manufacturing process. Training courses on the technology, the selection of the plastics, optimisation of the process parameters and postprocessing steps and support with the regulatory requirements also form part of the Kumovis package, allowing patient-specific implants to be available more quickly.
Your company’s quality management system was already ISO certified in 2019. What was your experience with the certification process – do you have any tips for other startups that aim to achieve certification?
For us, it was clear from the start that we were addressing a market that requires a high degree of responsibility and regulation. It was thus a logical first step to introduce a standard-compliant quality management system on market entry and continuously further develop it as the company grows.
I particularly see the ISO-9001 certification as an opportunity in the development of the company as it quickly allows an awareness of processes and interfaces and clarity in this regard to be established. The prerequisite is that the processes match the respective stage of the company. Adjustments are therefore constantly being made, above all in the early phase of company development. My tip here is to weigh up the opportunities and challenges of certification; it helps to clarify the workload and necessity with companies of a similar size and product range. If it is clear that certification will become necessary at some point, it’s worth tackling the topic at an early stage on market entry. This creates confidence among clients and investors.
Alongside the skull implant that you currently offer, what other products are you currently working on and what challenges are you facing?
The focus currently lies on market entry for our workflow for additively manufactured skull implants. Nevertheless, we are simultaneously working on other applications, such as probe implants for spinal fusion operations. Surgery uses them before inserting the final vertebral body replacement implant.
There are rules and learning curves at first, which are necessary on all sides when it comes to processes. What we are working on with medical technology companies and hospitals are additive manufacturing solutions that did not exist before. This brings with it challenges that range from material- and application-specific process parameters to invoicing procedures. The regulatory framework has also not yet been honed, so topics such as approval also take a great deal of time on our side – which is right and important. In the end, it’s ultimately about enabling patients to lead a better life.
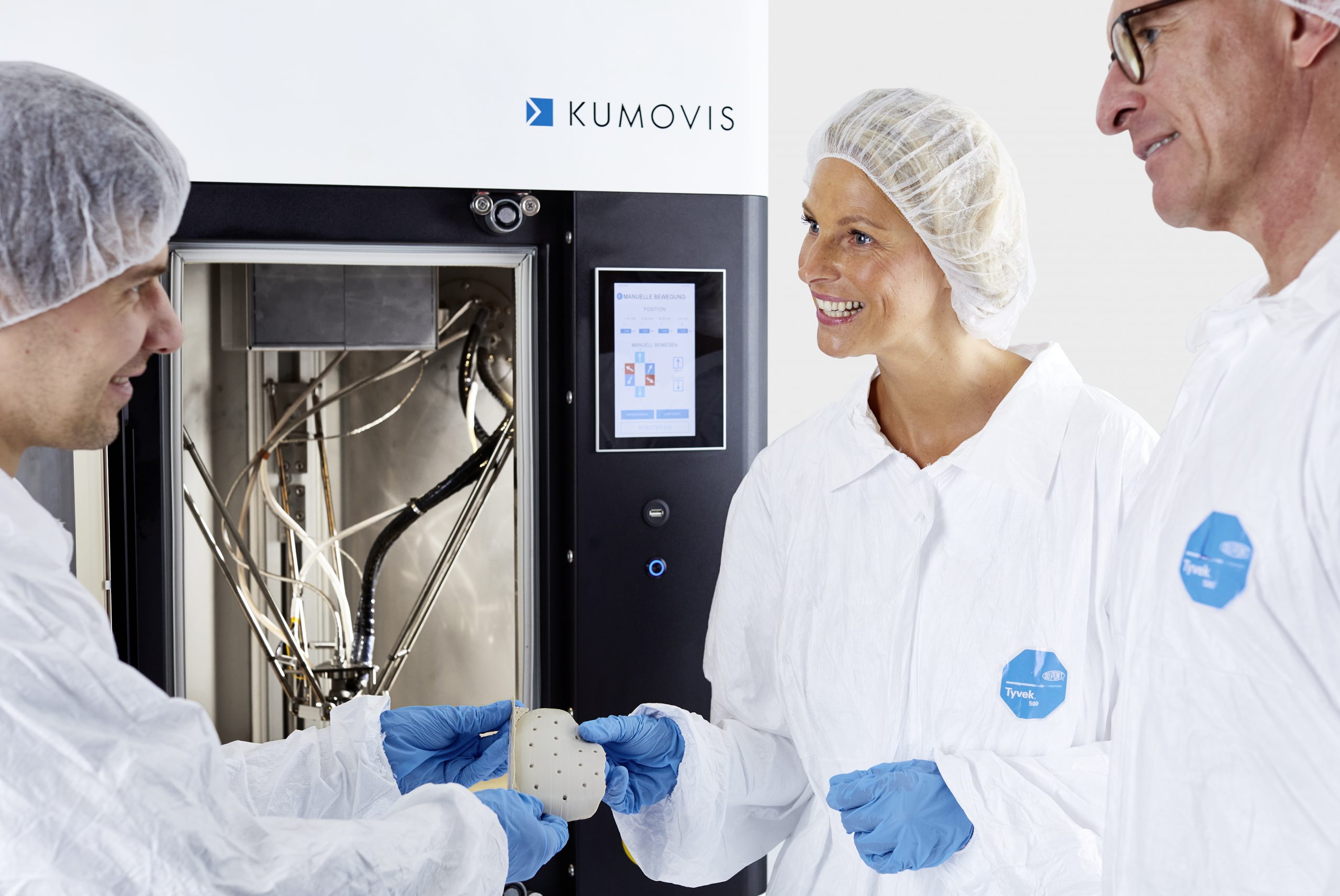
Kumovis recently also launched on the US market. What challenges do you expect in the health care system in the USA compared to Europe?
The complexity, intricacy and regional and treatment-specific features of the various health care systems are a huge challenge. Not just in relation to the USA, but also other European countries. This is one reason why we see our strength in the manufacturing process for medical products and focus on this. Our clients, however, specialise in marketing and distributing the finished medical products. A close partnership with clients is all the more important for both sides. Only in this way can new manufacturing solutions be integrated into a health care system as seamlessly as possible.
Will additive manufacturing become more and more important in the medical sector in the future? Will there soon be a Kumovis printer in every hospital?
Additive manufacturing opens the door to the economical production of small series and patient-specific implants. It allowing existing treatment options to be further developed. New ones can also be created: some applications can be made less costly and time-consuming with the help of our technologies and plastics, while others offer new advantages for patients that would not have been possible without 3D printing.
Nevertheless, it is clear that not every application, not every medical product, is a good fit with the manufacturing method. And so it will not be necessary to find a 3D printer from Kumovis in every hospital worldwide. The technique that we have developed will be used in medical technology on an equal footing as other techniques – such as injection moulding – from now on. With regard to quality, 3D printing is just as good as conventional manufacturing. Exciting times lie ahead.
Who or what is the most important thing in your company, without which Kumovis would no longer be able to operate?
The most important thing at Kumovis is the high level of motivation and openness among all of the employees. I dare to say that we all absolutely want to and are able to realise our shared vision of improving patient care with the aid of additive manufacturing. Here at Kumovis, we are thus united by a driver that is incredibly strong. It also makes us open to new, experimental things. Every idea is heard. This may be our greatest strength.
Comments are closed.